I have found very little evidence that wood turners used continuous rotation lathes prior to 1600, though pewterers and other metalworkers clearly did. In 1550 a lawsuit was brought against "old Peverell" because the noise from his "tornyng whele" was annoying his neighbors; but it is unclear if Peverell was a wood turner. The lack of continuous rotation lathes may have been due to the higher cost, the adequacy of pole lathes, or it may have related to guild restrictions. In urban areas such as London, guilds (or companies) restricted the tools and techniques that a craftsman could use. Even so, there were numerous disputes over who was entitled to use a lathe, and efforts to settle the dispute through company charters met with limited success.(10) Among rural craftsmen, restrictions were less stringent and individuals were more at liberty to practice multiple trades (or at least use their tools).(11) Among those craftsmen who observed guild restrictions, the work of a turner was marked by round mortises and tenons, pegged or wedged in place.(12) The cutting of square mortises and tenons was reserved for joiners, who might contract out the turning for a piece or, if skirting the restrictions, hire a turner to work in his shop or simply turn it himself.
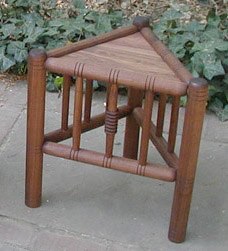



